Revisiting the Airworthiness Issues of the L-1011 TriStar Tanker: A Reflection on Engineering Growth
Introduction
In 2019, as a second-year aerospace engineering student, I conducted a research project under NAVAIR (Naval Air Systems Command) on airworthiness in aviation. My case study was the Lockheed L-1011 TriStar Tanker, a commercial airliner adapted for military use. Looking back, I now see how advanced methodologies could have deepened my analysis. Here, I reflect on what I’d do differently today, given my current engineering skills and understanding.
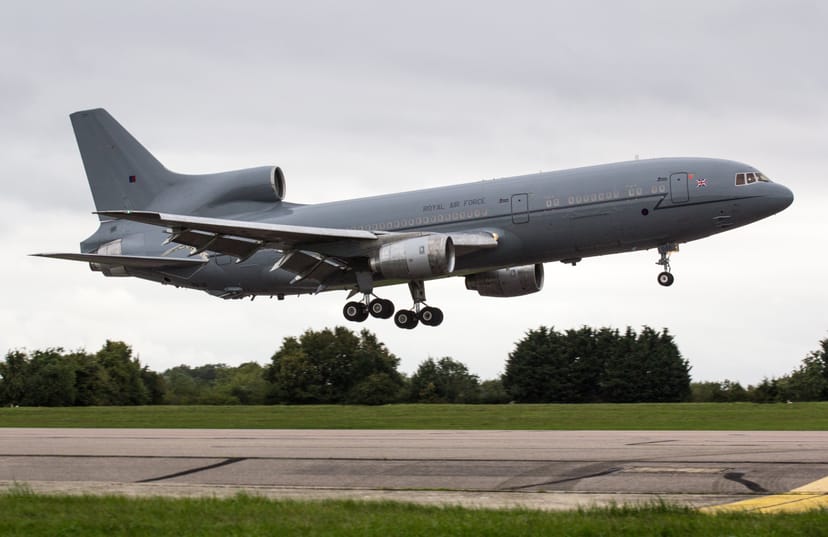
Understanding Airworthiness
Airworthiness ensures an aircraft’s operational safety by meeting FAA and EASA standards that cover structural integrity, system reliability, and performance. Over time, these standards have evolved to include probabilistic risk assessments and damage tolerance evaluations for long-term reliability. Understanding this evolution and the methods involved highlights the complexities of designing for airworthiness in both commercial and military applications.
The Lockheed L-1011 TriStar: Design and Development
Development Context and Challenges
The L-1011 TriStar, developed to compete with the DC-10, faced substantial setbacks, especially with the Rolls-Royce RB211 engine delays. The need to adapt under financial constraints significantly influenced design choices and airworthiness outcomes. Revisiting these economic pressures now, I recognize how they shaped the aircraft’s unique features and airworthiness considerations.
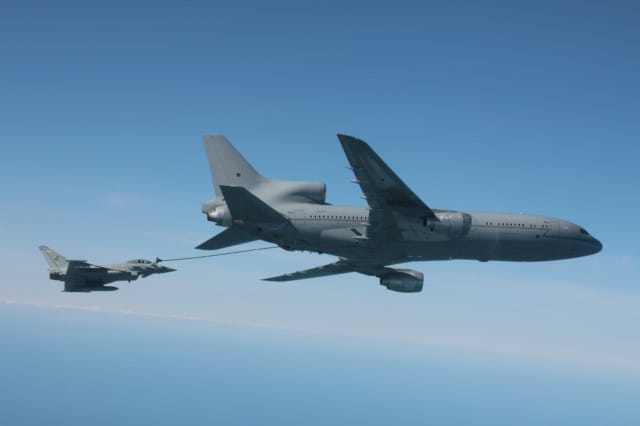
Figure 2: L-1011 TriStar performing air-to-air refueling operations, showcasing military adaptation capabilities
S-Duct Aerodynamic Design
The L-1011’s S-duct configuration for the third engine was an innovative solution to improve airflow and reduce noise. Modern Computational Fluid Dynamics (CFD) could simulate airflow patterns to assess how this design balanced efficiency with maintenance demands. Simulating this design today could provide insights into the aerodynamic trade-offs faced during development.
Revisiting My 2019 Research: Gaps and Updated Approach
Original Approach and Identified Gaps
Initially, my research focused on summarizing secondary sources without deep technical analysis. With my current knowledge, I recognize three major gaps:
- Lack of Quantitative Analysis: I did not incorporate quantitative methods like Finite Element Analysis (FEA) or CFD simulations, which are essential for an engineering study.
- Narrow Resource Base: I relied on limited data sources rather than primary materials, such as flight logs or structural test reports, which would have provided empirical insights into the aircraft’s operational history.
- Overlooked External Factors: I missed the broader context, including economic and regulatory influences, which are critical in shaping design decisions and airworthiness standards.
How I Would Approach the Research Today
With my current skills, I would approach the L-1011’s airworthiness issues from multiple angles:
- Finite Element Analysis (FEA): Using FEA, I could analyze structural reinforcements and stress points specific to the tanker version, especially where military modifications affect load-bearing capacity. This would provide quantitative insights into structural integrity under varied operational loads.
- CFD Simulations: To understand the S-duct’s impact on performance, I’d use CFD tools to simulate airflow and identify areas of drag or flow separation. These simulations would help analyze the balance between aerodynamic efficiency and engineering complexity
- Primary Data Analysis: Accessing flight logs, maintenance records, and incident reports would enable a robust data-driven approach. These records reflect the L-1011’s practical airworthiness issues and provide an empirical foundation for assessing its operational history, a cornerstone of any airworthiness study.
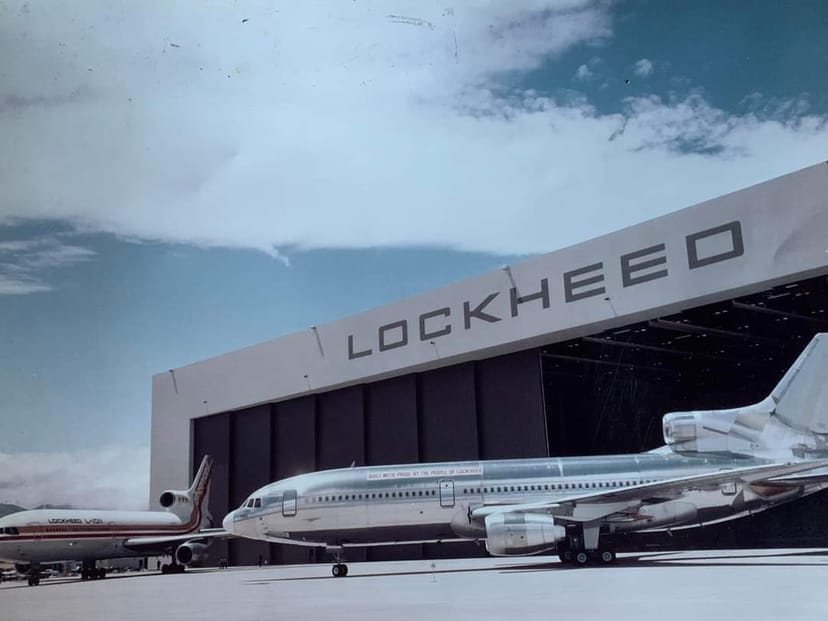
Figure 3: L-1011 TriStar at retirement, illustrating the end of its operational service and the importance of long-term airworthiness considerations
Reflecting on My Growth as an Engineer and Future Direction
Revisiting the L-1011 TriStar project has highlighted the progress I’ve made in engineering analysis and research methodologies. I now see how advanced tools like FEA, CFD, and primary data analysis add depth and rigor to airworthiness studies, underscoring the importance of a data-driven approach in aerospace. This experience has not only strengthened my commitment to continuous learning but also sharpened my focus on innovation in engineering.
References
-
Federal Aviation Administration (FAA), “Advisory Circular 25.571-1D: Damage Tolerance and Fatigue Evaluation of Structure,” Federal Aviation Administration, Washington, DC, Dec. 2014. [Online]. Available here
-
European Union Aviation Safety Agency (EASA), “Part 21 - Certification of Aircraft and Related Products, Parts, and Appliances,” EASA, Cologne, Germany. [Online]. Available here
-
J. E. Hawkes, “Development status of the L-1011 TriStar,” SAE Technical Paper 710755, presented at the National Aeronautical and Space Engineering and Manufacturing Meeting, Feb. 1, 1971. [Online]. Available here
-
NASA Dryden Flight Research Center, “L-1011 in flight - Wing vortex study,” NASA Dryden Photo Collection, Edwards, CA, Photo No. ECN-7848, Jul. 20, 1977. [Online]. Available here